GAS ASSISTED INJECTION MOULDING
Gas Assisted Injection Moulding (GAM) is a technology in plastic injection moulding that offers opportunities to reduce moulding costs, improve quality and allows designers to be even more imaginative in the creation of injection moulded components.
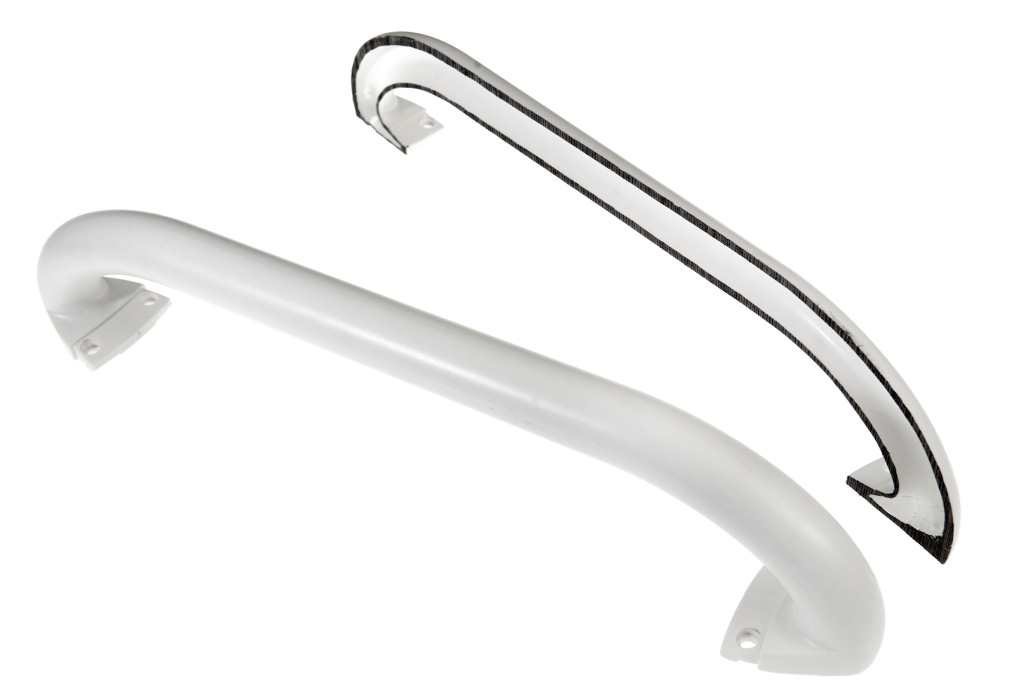
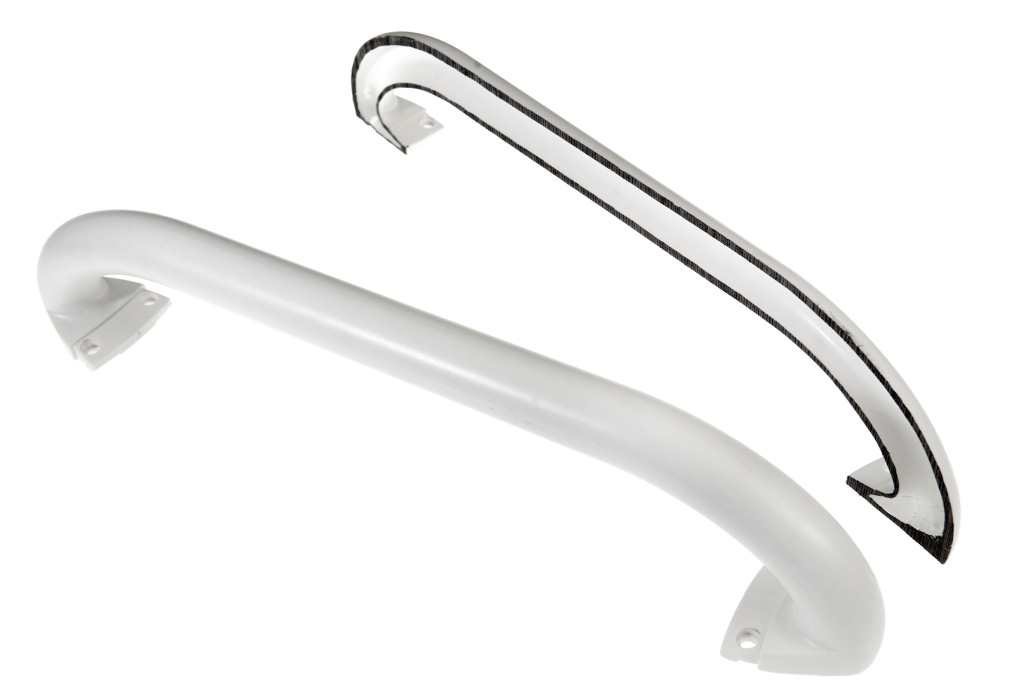
Gas assisted moulding involves the introduction of nitrogen under pressure to the mould cavity at a set time during the moulding cycle. The aim is to either hollow out thick section mouldings or eliminate sinkage and/or warpage in thin section injection mouldings. Gas injection can also result in stronger parts due to the ‘box section’ effect.
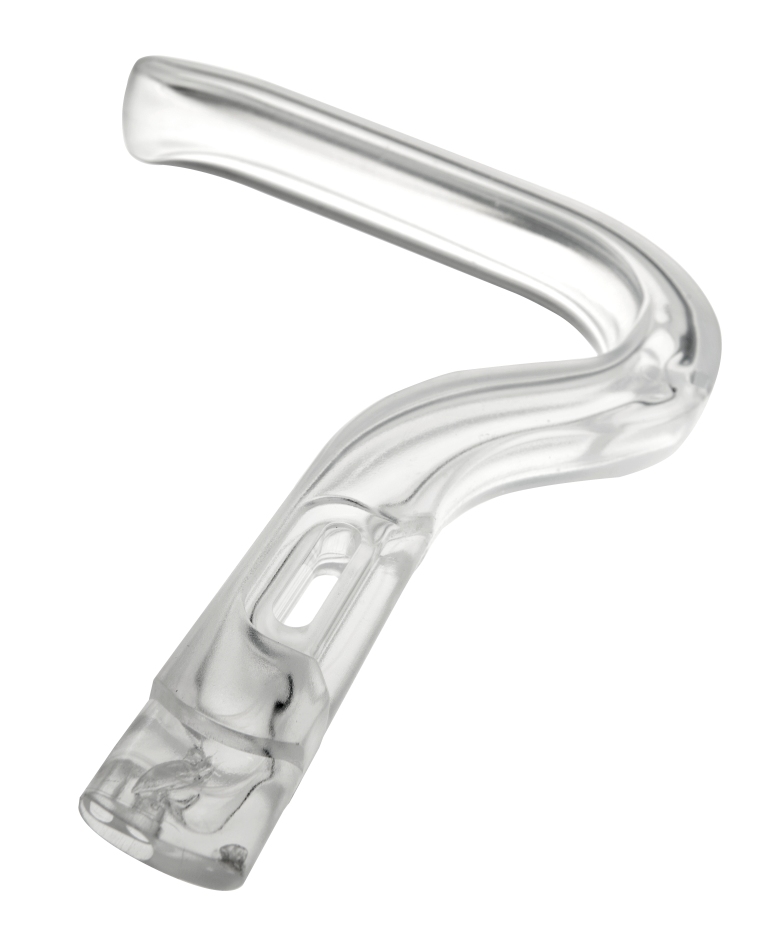
COST REDUCTIONS
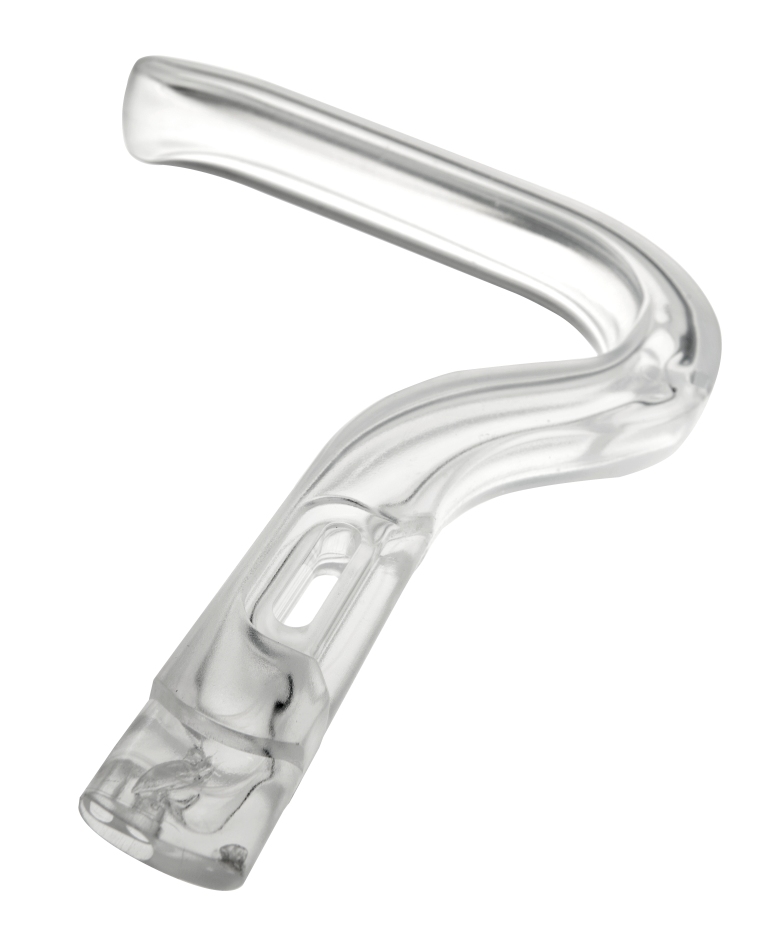
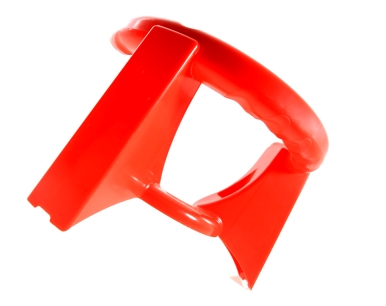
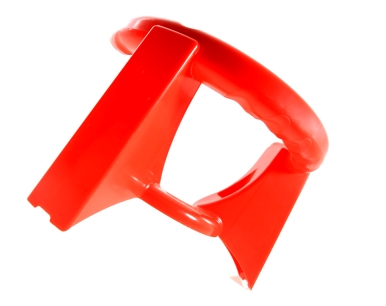
IMPROVED QUALITY
GAM IMAGINATION
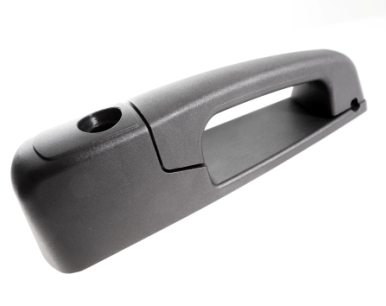
PLASTIC GAS INJECTION MOULDING APPLICATIONS
There is now a wide variety of injection moulded applications for gas assisted injection moulding. Not just thick section mouldings that require hollowing out, but many thin section applications also.
Apart from different types of handles for all industries, GAM is also used in the automotive industry for engine parts, internal and external trim and instrument panels among other things. Less obvious uses are front bezels and rear covers for TV cabinets, base frames for washing machines, shower heads, plumbing fittings and even strengthening ribs for plastic pallets.
The list is growing all the time with new gas injection applications being added on a regular basis. Material choice is not a constraint as gas injection moulding can be used with the majority of polymers.
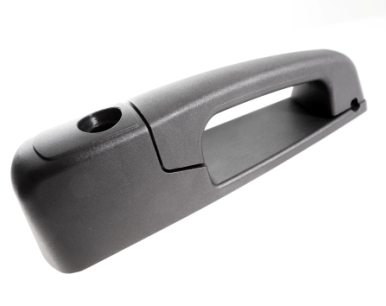
REASONS FOR THE DEVELOPMENT OF GAM
The use of conventional moulding techniques when attempting to produce thick sectioned mouldings has always proved problematic. The sink marks that occur due to contraction of the polymer cannot be completely compensated by the inflow of additional molten plastic. For this reason, the question of how these sink marks could be reliably avoided was investigated.
Processes such as low pressure structural foam moulding, gas counter-pressure injection moulding and co-injection moulding were developed to avoid sink marks that occurred during the manufacture of thick walled thermoplastic mouldings.
During gas assisted moulding, or gas injection moulding as it is sometimes referred to, Nitrogen is injected into the molten centre of the part with the objective of counteracting contraction during cooling by means of the internal gas pressure inside the moulding. With this process, mouldings can be produced that are free of sink marks where conventional processing may fail to achieve the desired quality level.
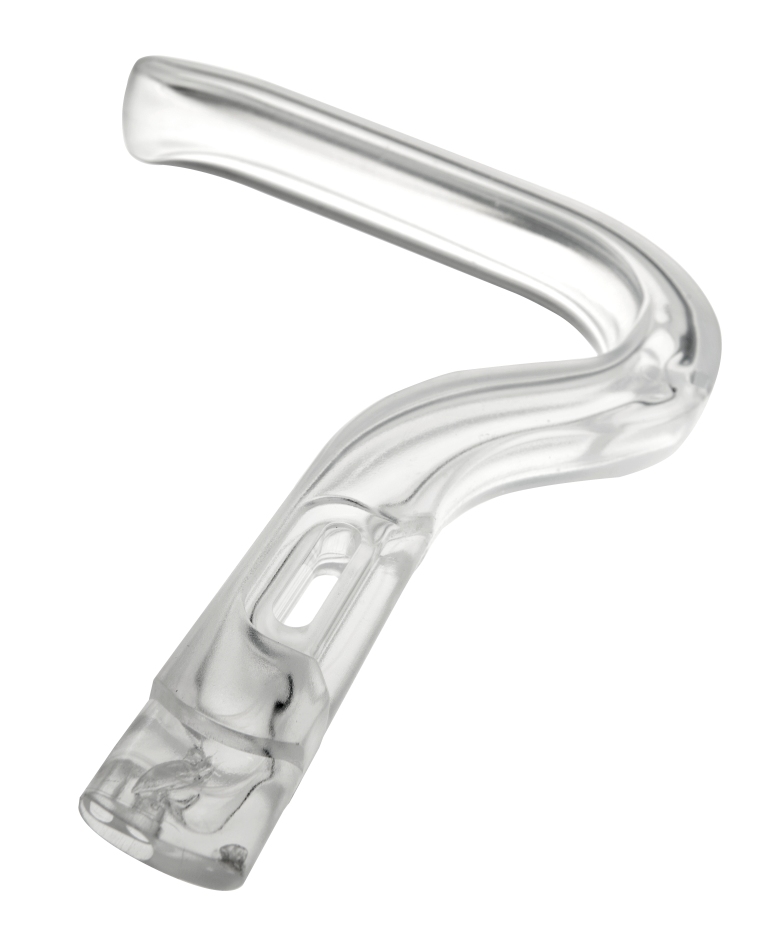
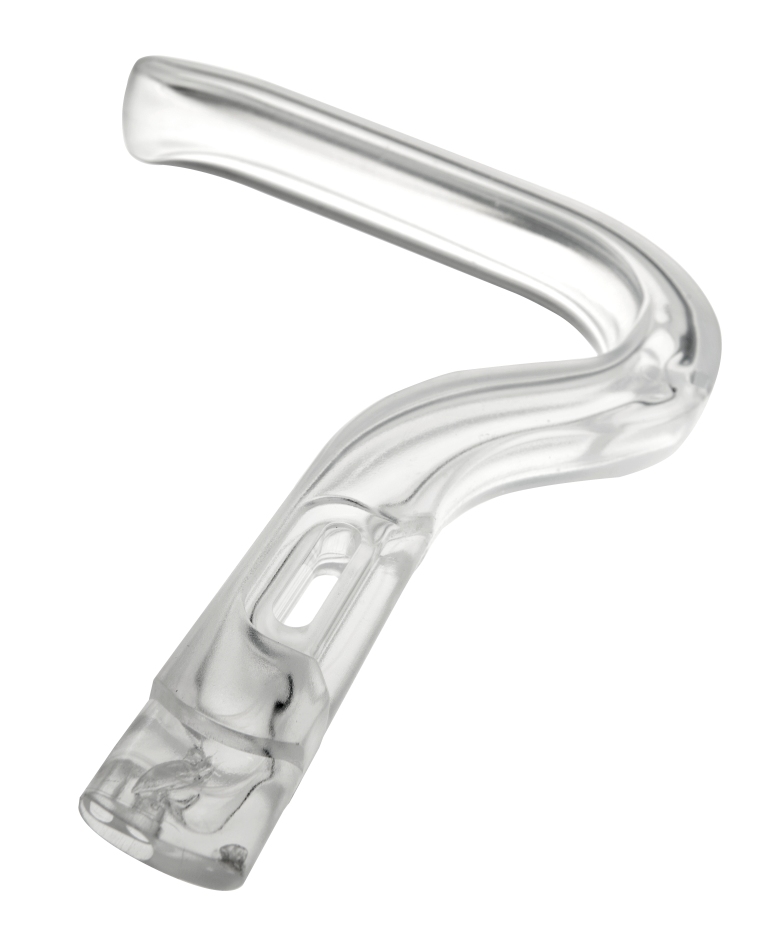
FIELDS OF APPLICATION
The production of mouldings with controlled hollow sections offers advantages to the injection moulder and designer. To evaluate and quantify the possibilities and benefits available from the use of this process it is necessary to divide the applications into different product groups according to their generic shape.
ROD SHAPED MOULDINGS
This group includes all mouldings that resemble the shape of a rod or handle. For these mouldings, the gas-assisted moulding process offers decisive advantages, including:
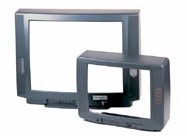
PANEL SHAPED MOULDINGS
Thin walled panel shaped mouldings often cause difficulties in standard injection moulding. Due to the large projected areas, high clamping forces are necessary and parts tend to warp due to high internal stresses. The design guidelines for the conventional injection moulding process set limits to the obtainable stability and rigidity of the mouldings.
Here, GAM offers further advantages. In order to conduct the gas, channels of sufficient cross-section must be provided. These channels must have cross-sections wider than conventional ribs and can also be designed deeper, not only to conduct the gas but to provide additional rigidity for the part. Since gas pressure is effective down to the end of the flow path because of the hollow ribs, it not only counteracts sink marks but allows the mould to be filled at a lower pressure.
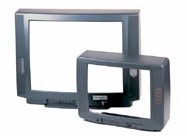
The low cavity pressures lead not only to lower internal stresses and thus to a lower warping tendency, but also allow the mouldings to be produced at much lower clamping forces. As a general rule, clamping forces can be assumed to be 25% to 50% of the normal values used in conventional injection moulding.
General advantages for panel shaped mouldings can be summarised as:
It is important to consider at the design stage the path of the gas. The gas will always follow the line of least resistance; therefore the design of any rib structure must be such that the path of the gas is repeatable shot after shot.
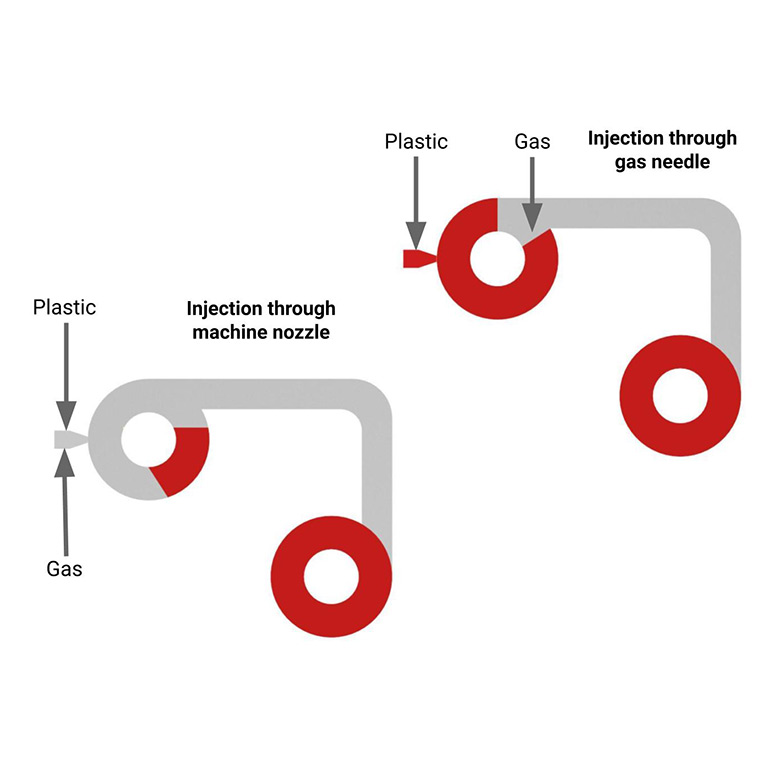
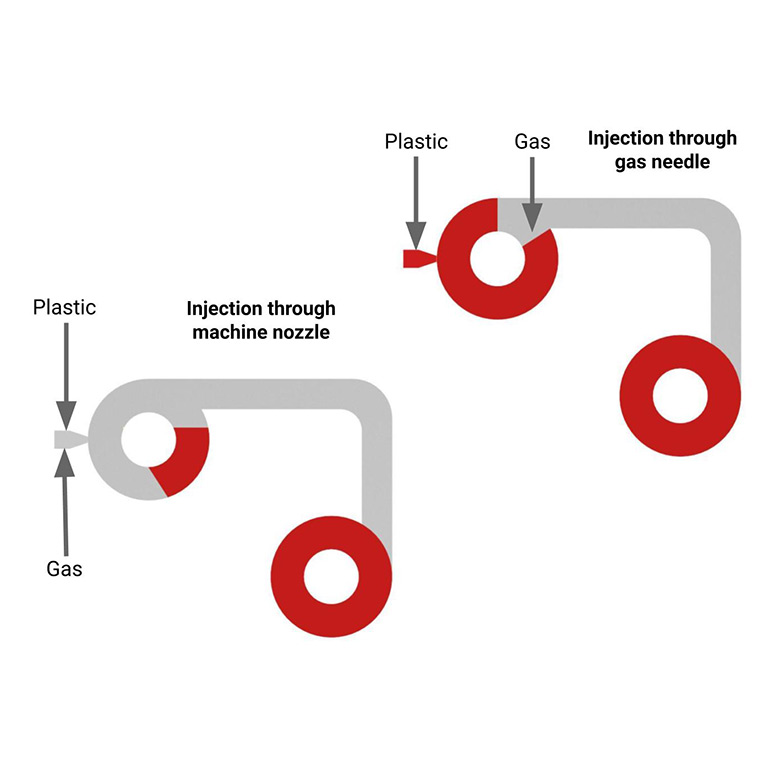
OVERVIEW
There are a number of different versions of GAM. For hollowing out parts the two most common approaches are: short shot and overflow method. The former involves partially filling the mould with molten plastic and then using the nitrogen gas to effectively blow the part up like a balloon. In the overflow method the mould cavity is completely filled with plastic and the, once a skin has formed, using the nitrogen gas to expel the molten plastic from the centre of the part into an overflow chamber.
There are different approaches to this latter method as well. Rutland Plastics would be happy to advise on the most suitable method for your particular application.
The majority of polymers can be used with gas assist injection moulding, including glass and talc filled plastics.