PLASTICS ADDITIVES
Why do we use additives in plastics?
Please Note: This page is for information purposes only. Rutland Plastics is an Injection Moulder and does not supply plastics additives.
To ease processing
It is important that the molten plastic forms the product desired without changing colour, sticking in the mould or suffering some other problem. Process aids are used to ensure the result is what is expected. They can aid the mixing of pigments ensuring an even distribution of colour.
Other additives can make the plastic particles adhere more to each other so that they melt more quickly resulting in lower moulding temperatures so reducing the risk of heat damage to the polymer.
Lubricants can be used where the plastic material is viscous once melted. Antioxidants may be added to prevent embrittlement or discolouration of the plastic when melted. Similarly, heat stabilisers may be used to stop the plastic material from decomposing during processing.
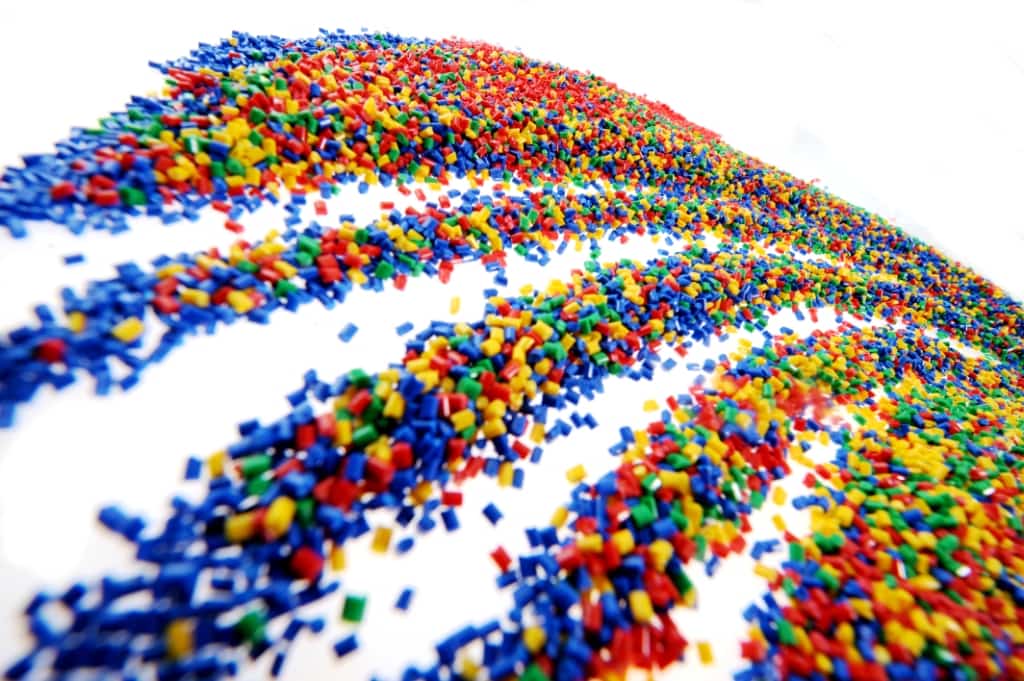
Improving appearance
Certain plastic objects may be painted but most are coloured during the moulding process. This means the colour can never wear off as the part is coloured throughout. It is also possible to match the colour to other objects, even if they are made from a different material. Some special effects, such as metallic sparkle or woodgrain, are also possible.
Saving Money
Plastic products may be produced without the use of expensive additives enabling them to be sold more cheaply. The consumer may not be aware of these particular differences but the life of the product could be much less than a more expensive alternative. For example, the more expensive product may contain an impact modifier making it less likely to be damaged if it were accidentally dropped or knocked against another hard object.
A cheaper electrical product may not contain a flame retardant which could be dangerous.
Other additives may reduce the overall cost of a polymer, including mineral fillers such as talc and chalk. However, the main reason for adding these is to increase rigidity rather than lower cost. These types of filler can also reduce moulding cycle times so lowering production costs.
Improving safety
Flame retardants have already been mentioned. These are obvious safety related additives. Impact modifiers have also been mentioned as a means of increasing strength of a moulding. However, they can also have a safety aspect. Car dashboards need to absorb the force of impact in order to reduce injury. An impact modifier would be used to help the material achieve this objective.
Pigments can also be used for safety, bright and fluorescent colours on safety equipment, for example.
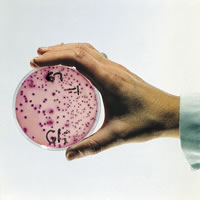
Hygiene
Plastic materials are widely used in medical applications as they are clean and disposable. Various additives are used, such as antimicrobials, to improve the hygiene of the product.
Additives may also be introduced to enable food containers to be used in both freezers and microwaves without becoming brittle or melting. It should not be forgotten that cling film is also a plastic, this prevents bacteria from getting to the food.
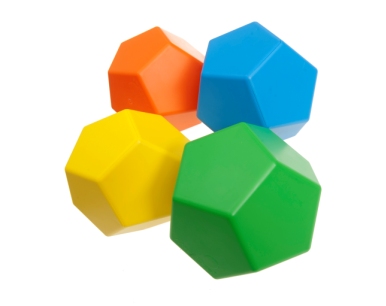
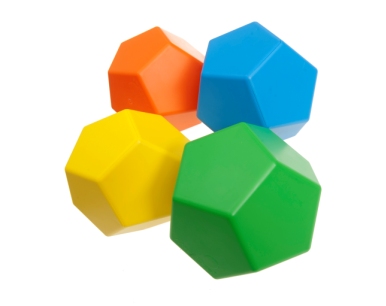
Longer life
An increasing number of automotive components are now made from plastic. Garden furniture and stadium seats are also largely plastic nowadays. All of these are exposed to the elements year round. UV Stabilisers and antioxidants lengthen the lives of these products, without these additives the products could soon lose their colour and become brittle.
Better for the environment
Much is made of the fact that plastics consume energy in their manufacture and are difficult to dispose of. However, positive impacts include the saving of fuel – the increased use of plastics in cars has reduced their weight and helped to increase their fuel economy.
Crop yields are boosted by laying plastic film over the soil to trap heat and moisture. Additives allow the sheet to disintegrate as soon as the harvest arrives.
Plastics can be recycled into fencing, pallets and road markers, for example.