PLASTICS ADDITIVES – FILLERS
There are a number of different fillers that can be added to polymers, but we are concerned here with particulates, of which there are two types: inert and reinforcing.
Please Note: This page is for information purposes only. Rutland Plastics is an Injection Moulder and does not supply plastics additives.
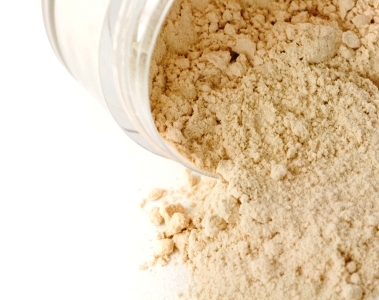
INERT FILLERS
Inert fillers will increase the stiffness and hardness of a plastic. They will also usually reduce the cost of the compound as they are generally cheaper than the base polymer. Inert fillers that are most commonly used include calcium carbonate (chalk), talc and barium sulphate.
The shape and size of the particles is important. The smaller the particles the higher the values of properties such as tensile strength, modulus and hardness. Coarser particles can give compounds less strength than an unfilled material.
Reinforcing fibres include glass and carbon, with the latter being used in specialist applications. The purpose of using these fillers is to improve the strength and heat resistance of a polymer.
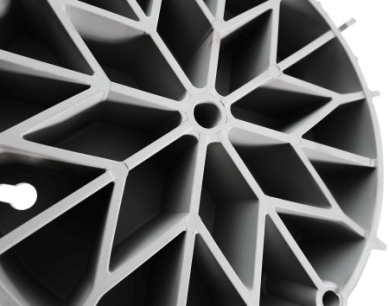
WHY ARE FILLERS USED?
For the remainder of this article, we shall concentrate on glass as a filler as this is the most widely used and offers the greatest benefits in the enhancement of polymer properties.
A major area of growth in the use of plastics is as a metal replacement. However, thermoplastics have the following disadvantages in comparison with metals:
- Low rigidity and tensile strength
- Dimensional instability as a result of a high temperature coefficient of expansion and high water absorption
- Low maximum service temperature
- Low impact strength
- Low hardness and scratch resistance
- Low creep resistance
The addition of glass fibres can improve all of the above properties. For example, a long strand glass coupled polypropylene (glass fibre strands as long as the polymer granules) will have 3 times greater tensile strength and 4 times greater rigidity at room temperature than an unfilled grade. This rises to 4 times and 8 times respectively at 100C.
Similar results will be seen with glass filled nylons which are more commonly used as metal replacements.
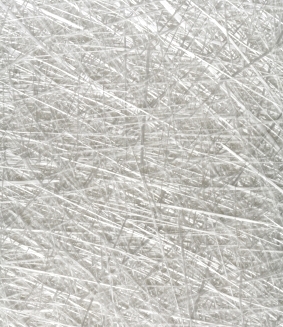
GLASS FILLERS EXPLAINED
Most glass fillers are short strands of glass fibre but there are an increasing number of long strand grades becoming available. The long strand versions can provide greater strength over the more traditional short strand varieties. It should be stressed at this point that the design of the part will still have a big impact on the final strength as the orientation of the fibres will be affected by the flow of the material. Also, the injection moulding process will break some of the fibres, particularly in the case of long strands.
A coupling agent may be used to improve adhesion between the fibres and the polymer. This results in a more even distribution of the fibres which is retained during the moulding process. As a result, coupled materials, as opposed to filled, will often demonstrate higher impact strength properties.
There are also nylons filled with glass beads. These will improve compressive strength, heat deflection temperature, tensile strength and modulus (stiffness) when compared with unfilled grades. Furthermore, when compared with glass fibres they are easier to process, have uniform and predictable shrinkage and minimum warpage.