PLASTICS ADDITIVES – UV STABILISERS
Most plastics degrade over time when exposed to UV (Ultra Violet) light. This leads to colours fading and the material becoming brittle.
Please Note: This page is for information purposes only. Rutland Plastics is an Injection Moulder and does not supply plastics additives.
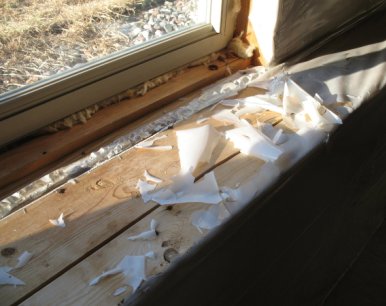
Addition of a stabiliser is required to extend the life of the part if it is to be exposed to UV light. For black parts carbon black is generally used to colour them. As carbon black absorbs UV light, black products often display the best long term performance when used outside.
There are two main types: UV absorbers and UV stabilisers.
UV Absorbers
These were the first type of protectors for polymers. As the name suggests, the chemicals ‘absorb’ UV radiation. These are most effective in thicker sections as there is a greater chance of the light energy falling on an absorber molecule. A relatively large amount of absorber needs to be added to ensure there is sufficient to absorb the light energy.
UV Stabilisers
The most effective are Hindered Amine Light Stabilisers (HALS). Instead of absorbing the light energy they interrupt the photodegradation before it starts. There is a variety of types available:
- Monomeric HALS – Small molecules which migrate readily to the surface
- Oligomeric HALS – Large molecules that remain relatively fixed within the substrate. For this reason these tend to be used in food contact applications
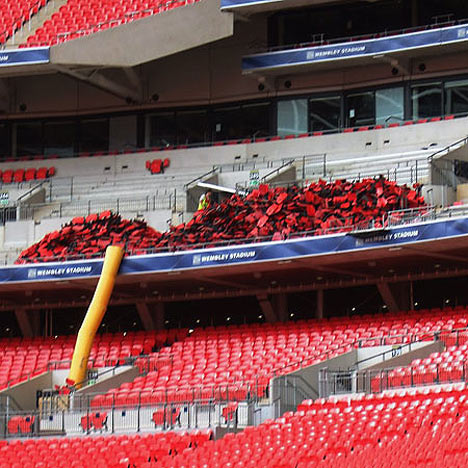
It is important to specify where in the world a final product will be used and its required life span due to variations in the intensity of sunlight.
Not adding a UV Stabiliser, or the correct levels of an appropriate additive, can have costly consequences. This was perfectly illustrated by the need to replace large numbers of seats at the new Wembley Stadium due to them fading to pink from red. These seats could also have become brittle in time with serious consequences for spectators.