BLOW MOULDING
There are two main forms of Blow Moulding – Injection and Extrusion.
Please Note: This page is for information purposes only. Rutland Plastics is an Injection Moulder and does not offer blow moulding services.
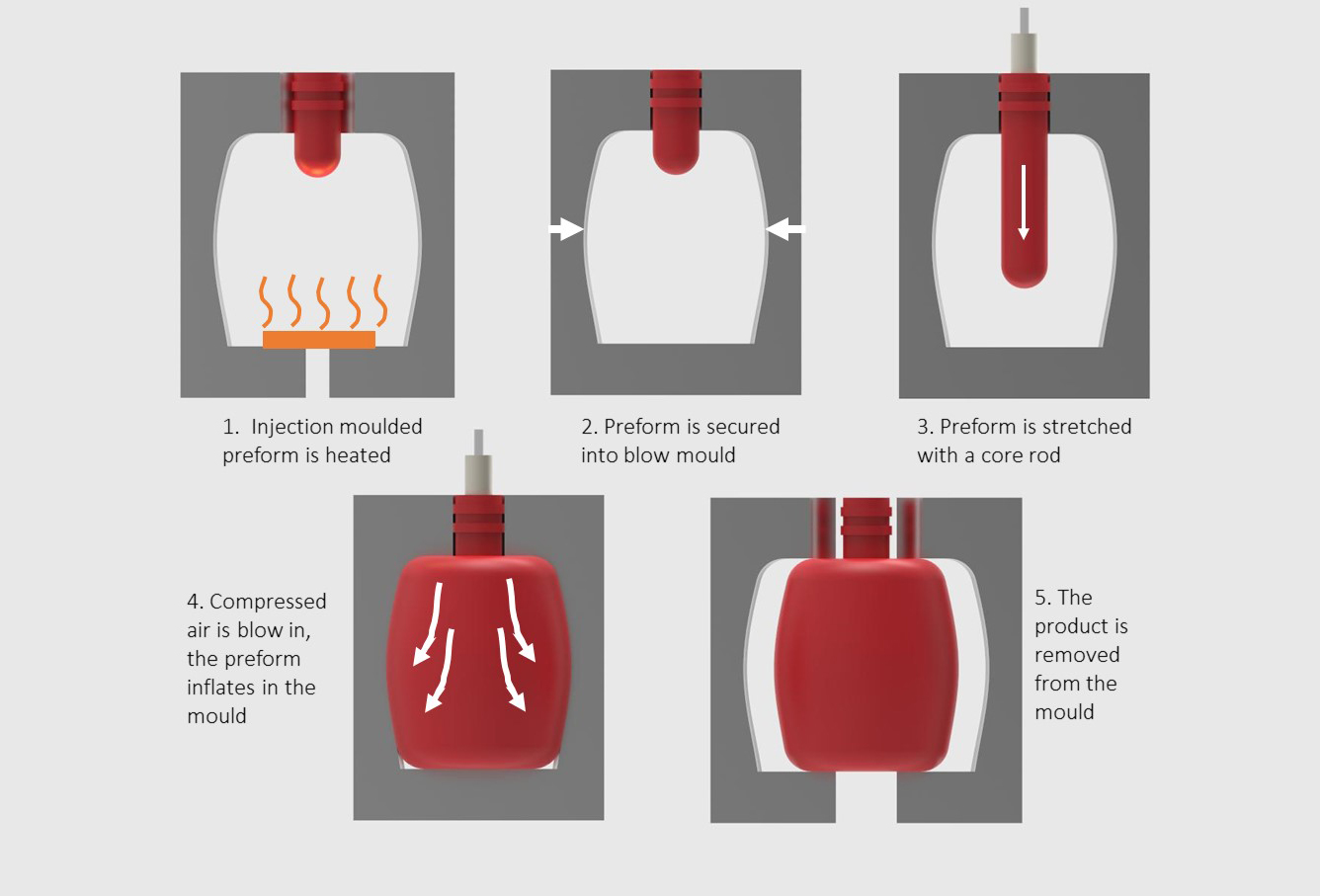
INJECTION BLOW MOULDING
Injection blow moulding is used for manufacturing large quantities of hollow parts, e.g. bottles, jars and other containers. There are three stages to the process – injection, blowing and ejection.
Injection – First a perform needs to be made. Molten plastic is injected into a hollow, pre-heated mould which forms the external shape. This is clamped around a mandrel (core rod) which forms the internal shape. This perform is produced with a fully formed neck of the bottle or jar.
Blowing – The mould opens and the core rod is clamped into a chilled blow mould. The core rod opens allowing compressed air into the perform inflating it to the finished shape.
Ejection – Once cooled the mould opens and the finished item is stripped off the core rod. As with injection moulding, the perform and blow moulds can have multiple cavities.
MATERIALS
The materials used for blow moulding include Polyethylene (High Density, Low Density and Linear Low Density), Polypropylene, Polyethylene-Terephthalate (PET), and PVC.
APPLICATIONS
- Bottles
- Jars
- Containers (including large drums of 50L and more)
All of the above for food and drink, cosmetics, garden and DIY.
EXTRUSION BLOW MOULDING
The process is similar to injection blow moulding with the exception that the mould for the products is filled with the required amount of molten plastic from an extruder. Air is then used to inflate the plastic to the required shape in the same mould.
Materials and Products are as for injection blow moulding.
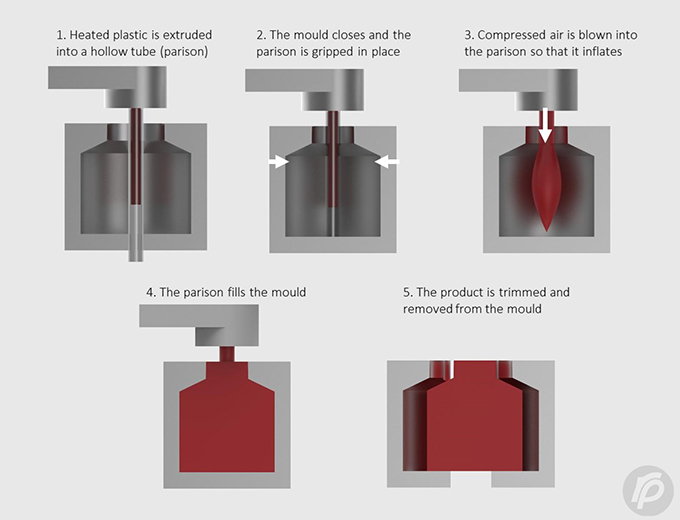
EXTRUSION BLOWN
Molten plastic is extruded through a die, usually vertically, forming a thin walled tube. Air is introduced through the centre of the die to blow up the tube like a balloon.
This extrusion continues upwards, cooling as it goes, and then passes through rollers to produce what is referred to as lay flat tubing. This can be kept in this form or have the sides slit to produce sheets. Lay flat tubing can be formed into bags by sealing and cutting at predetermined positions.
APPLICATIONS
- Film
- Plastic sheets
- Plastic bags