COMPRESSION MOULDING
There are a number of methods but the process is broadly similar. This is a process for the moulding of thermosets and differs from injection moulding in that the mould is heated to form the part rather than cooled to solidify it.
Please Note: This page is for information purposes only. Rutland Plastics is an Injection Moulder and does not offer compression moulding services.
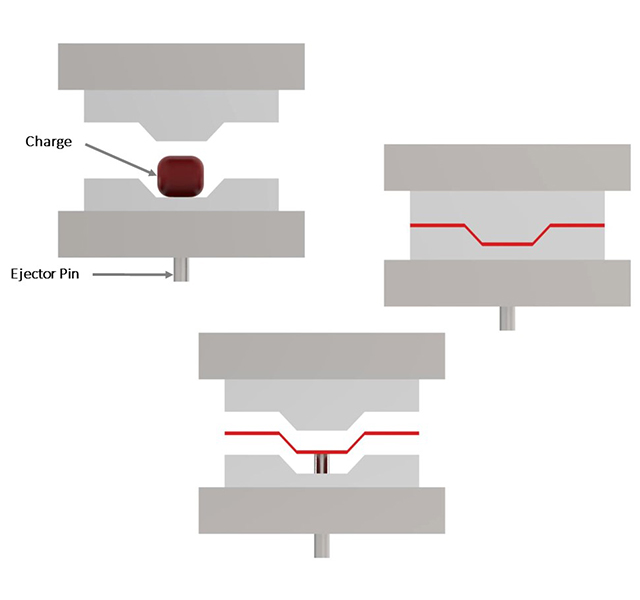
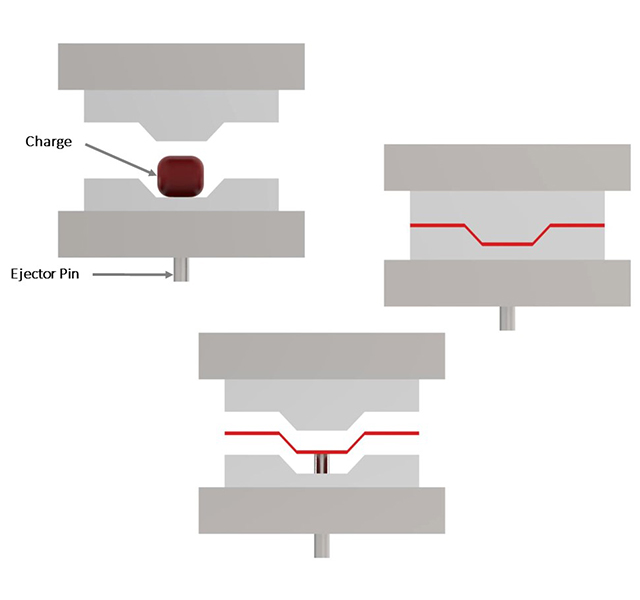
DOUGH MOULDING
The most common method is Dough Moulding Compound (DMC) or Bulk Moulding Compound (BMC). Thermosetting resins are used in a partially cured state, either in the form of granules, putty-like masses or performs.
The preheated material is placed directly into a heated mould. The material is forced into all cavities when the mould is closed with a top force. Heat and pressure are maintained until the material is cured.
SHEET MOULDING COMPOUND (SMC)
Another method is Sheet Moulding Compound (SMC). This process involves placing a reinforcing material, such as glass fibres, between layers of a thermoplastic and heating the materials so as to bond them together into a single sheet of material. This is then cut to size and reheated before being placed in a compression moulding press. This has a higher cost due to the handling and manufacturing costs in making the sheet. The material used in making the sheet is also heated three times – when making the initial thermoplastic sheet, then again when bonding with the reinforcement and finally, when making the part itself.
MATERIALS
Phenolics (“Bakelite”), some polyesters, urea formaldehyde, melamine formaldehyde.
APPLICATIONS
Applications where mechanical strength, electrical and thermal insulation properties are required.
- Electrical switches and sockets
- Radio and appliance knobs
- Electrical parts
- Automotive exterior panels (especially commercial vehicles)
ADVANTAGES
- Lower cost moulds
- Low material wastage
- Internal stress and warping are minimised
- Excellent dimensional accuracy and stability
- Thick and variable sections are readily achievable
- Large parts are practical
DISADVANTAGES
- Least product consistency
- Not suitable for fragile mould features
- Mould design problems where there are uneven parting lines
- High impact compounds make flash control and removal difficult
- Thermosets cannot be remelted like thermoplastics