Lighting
Thermoplastic materials are used in a wide variety of lighting and other electrical applications.
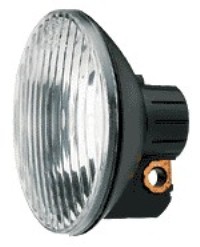
Housings – Selection would be based on which properties are required, for example, high heat distortion, high impact strength, weathering resistance. It could be just one of these or a combination. For low heat ABS, PC/ABS or Nylon; medium heat would require Polycarbonate or PPO and for high heat applications it would be necessary to consider PBT, PPO, Nylon or Polyetherimide.
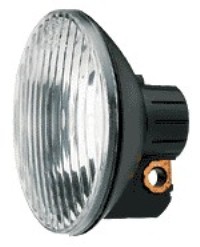
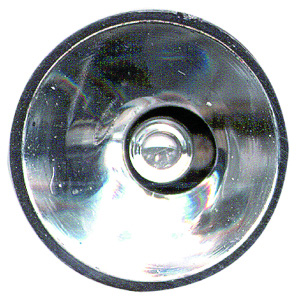
Reflectors – For fluorescent and low wattage lamps Polycarbonate offers a good range of properties. For vacuum metallised parts PBT, PPO and Polyetherimide all offer benefits.
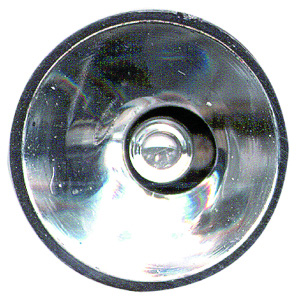
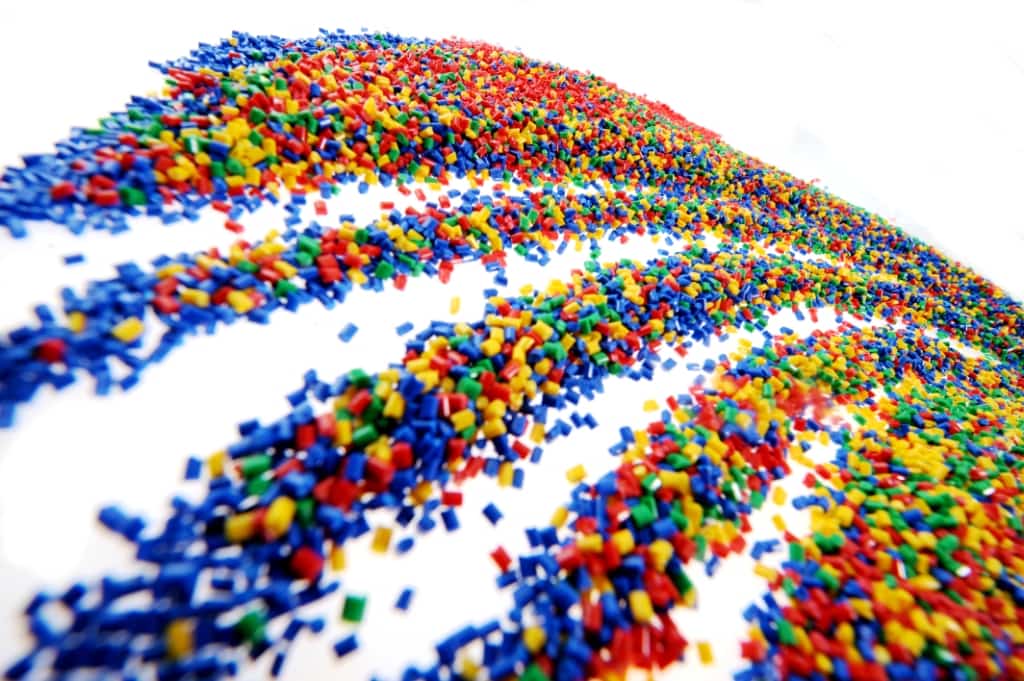
MATERIAL SUITABILITY
It can be seen that a wide variety of thermoplastic materials are used in lighting applications. Below is a brief summary of each of the materials mentioned, along with a couple of others that may be used in certain circumstances, and their key properties. More details can be found on the relevant materials page:
PC (Polycarbonate) – This material is used because of its exceptional clarity, high heat resistance and excellent toughness. It also possesses good chemical and scratch resistance. Acrylic tends to be more often used because it also has crystal clarity and a superior UV stability as well as being lower cost. Polycarbonate is used in applications where there is a need for damage resistance.
ABS (Acrylonitrile Butadiene Styrene) – Offers toughness, the ability to mould with tight tolerances and with minimum warpage.
PC/ABS (Polycarbonate/Acrylonitrile Butadiene Styrene) – This blend combines the low temperature impact resistance of ABS with the high heat resistance and toughness of Polycarbonate. It has the ability to withstand extremes of temperature and rapid, repeated temperature fluctuations.
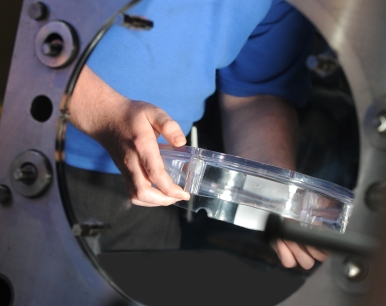
SAN (Styrene Acrylonitrile) – This material combines the strength and stiffness of Styrene with the heat and chemical resistance of Acrylonitrile. Although Acrylic offers superior UV stability in direct sunlight the majority of lighting applications are interior use and UV stabilised SAN is resistant to yellowing from man-made light sources. SAN can offer a stronger part than Acrylic at similar thickness. The optical properties of the two materials are similar although SAN does not possess the same water whiteness. SAN demonstrates better diffusivity in hiding bulbs and also provides amore even light distribution for improved aesthetics. It also offer better chemical resistance and heat distortion properties than Acrylic.
PET (polyethylene Terephthalate) – Often used as a replacement for metal light housings as it offers corrosion resistance and with the use of colour and textured surfaces has a better appearance. Excellent high temperature stiffness and strength, together with good weathering properties. Also used for reflectors and bezels in both indoor and outdoor applications, and lamp sockets.
PA (Nylon) – High temperature resistance, high strength and toughness. Also resistant to weathering and offers low warpage.
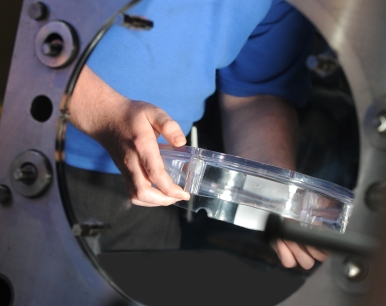
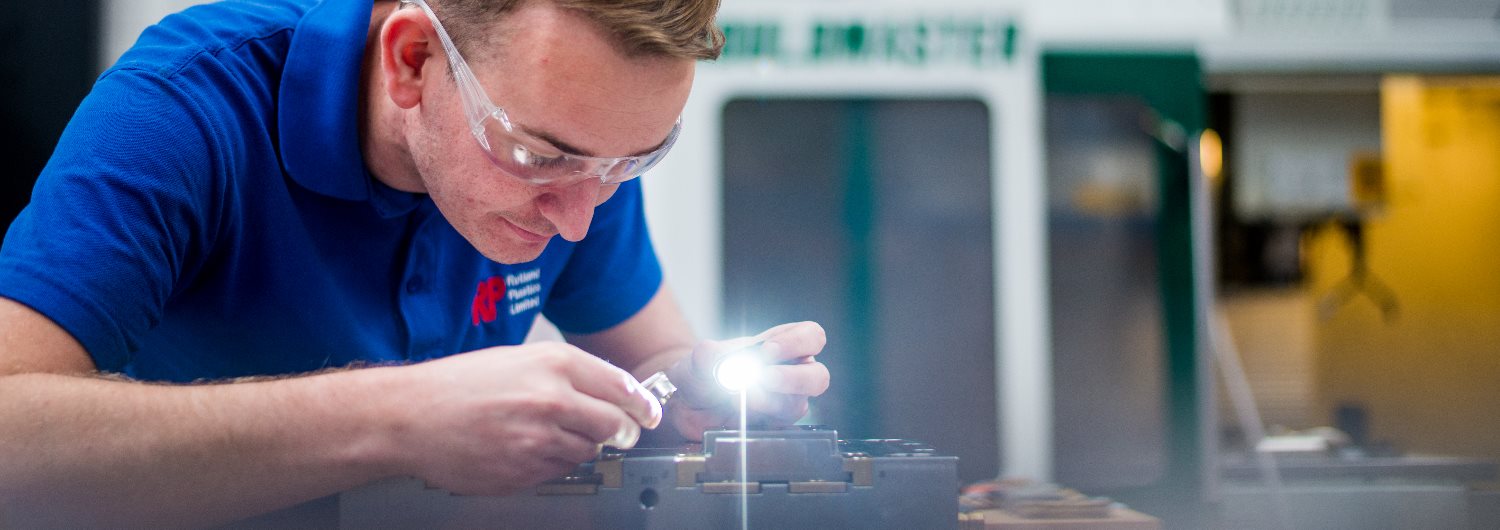
MATERIAL SUITABILITY
PBT (Polybutylene Terephthalate) – Used as an aluminium replacement in some applications because it can be easily coloured and offers cost reductions as there is no need for secondary operations. Once again, this material has good weatherability and high temperature resistance. Applications include street lamp housings and spotlight bodies.
PPO (Polyphenylene Oxide) – Good load bearing characteristics and dimensional stability at high temperatures.
PEI (Polyetherimide) – High strength. Performs in continuous use up to 170˚C.
LCP (Liquid Crystal Polymer) – Very expensive and extremely specialised. Highest heat distortion temperature of any thermoplastic. Outstanding strength at extreme temperatures and resistant to virtually all chemicals, as well as weathering, UV radiation and burning.