METAL REPLACEMENT
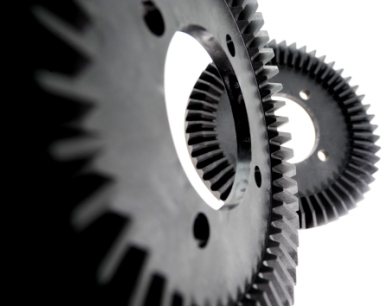
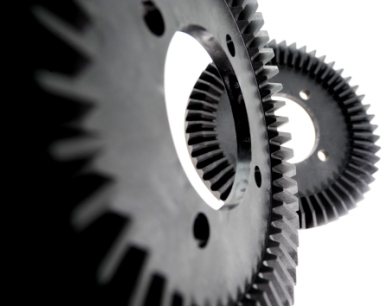
There are a number of reasons to consider plastics in place of metal:
Weight Saving. Thermoplastics are approximately 1/7th the weight of the majority of non-ferrous metals. The automotive industry has been a prime mover in the shift to plastics and, because of the volumes involved, the polymer producers have been driven to develop ever more advanced engineering grades with superior properties.
Cost Saving. This can take the form of lower actual material costs or lower production costs as it is usually cheaper to produce an injection moulded plastic part than its metal equivalent. Tooling costs for a moudled part may be higher but the production related costs can soon cover this. The lighter plastic part is also cheaper to transport.
Plastics do not corrode. Unlike metals and alloys, polymers do not oxidise. this can result in less maintenance, a longer life and a superior appearance.
Depending on the application, polymers offer additional benefits over metals, such as electrical insulation and sound deadening when parts come into contact. Where parts move against each other, such as gears, there can be less wear as some grades of polymer are self-lubricating. This also means additional lubrication is not required.
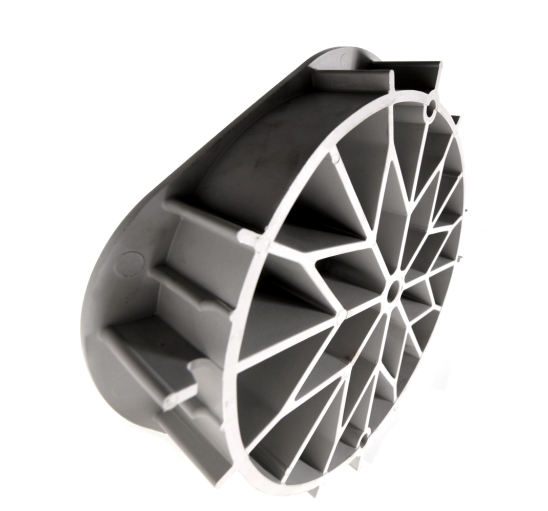
DIE-CAST PARTS
One of the prime candidates for replacement with plastics is die-cast parts. As already mentioned, there is an obvious weight advantage, but the injection moulding process also means that parts can be designed with better functionality. Another area of cost saving is the cycle time, the amount of time taken to produce a finished part, which is considerably shorter for parts produced using injection moulding.
Performance of the plastic part need not be an issue, modern thermoplastics, and in particular advanced Nylon grades, offer properties comparable to their metal equivalents. Admittedly, injection moulds are more costly than those for die-casting but they have a much longer life. Seven times longer on average.
Higher temperatures are not a problem as demonstrated by the large number of automotive under bonnet parts that are now manufactured in plastic. The strength of these thermoplastics is also illustrated by their increased use in powertrain and chassis components, such as clutches and steering.
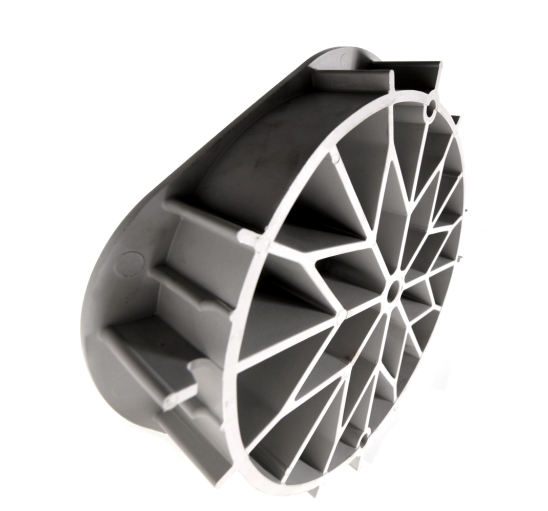
LONG GLASS FIBRES
Other developments in polymers include the use of long glass fibres. Some grades of long glass fibre filled polypropylene demonstrate similar properties to standard glass fibre filled grades of nylon, so reducing weight and cost against another traditionally used polymer.
See the separate article on Long Glass Fibre Filled Plastics.
Contact Rutland Plastics for advice on metal replacement.