Plating of Plastics - For information only
This page is for information purposes only. Rutland Plastics does not offer plating services but uses trusted suppliers to provide this service.
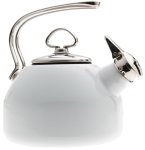
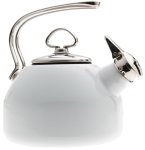
Metal plating of plastics can be carried out on virtually all types of resin. There are various methods:
- Vacuum metallisation
- Indirect metallisation
- Plating
- Painting
For the purposes of this article we shall focus on plating. This has become more widely used by a variety of industries both to save cost and weight, the latter is especially important to the automotive industry. Fashion is also an important factor as we have seen with the recent trend towards ‘chrome’ small domestic appliances.
There are many other benefits to plating parts:
- Protects the part from UV attack
- Acts as shield for electromagnetic radiation
- Prevents plastic part from absorbing water
- Can improve physical properties, such as tensile and flexural strength and the heat distortion temperature
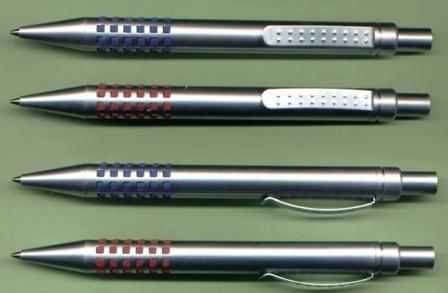
PLATING METHODS
There are two main types of plating: electroless, without the addition of electric current, and electro or chrome plating, when an electric current is used to produce a deposit of metal from a dissolved metal salt.
Electroless plating can be further divided into non-selective (the part is fully coated) and selective (only sections of the part are plated). With the latter a primer is sued instead of etching (see below).
As plastics are non-conductive, if the part is to be electroplated it needs to go through the electroless process first in order to deposit a conductive metal layer.
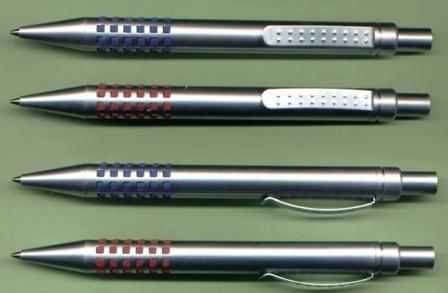
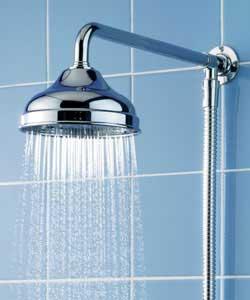
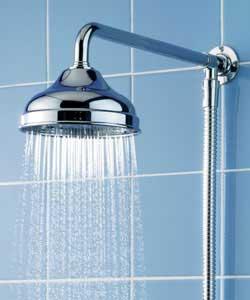
PLATING PROCESS
The general process is as follows:
Etching – The part is immersed in a tank containing concentrated chromic and sulphuric acid. This produces small holes on the surface of the part which will then hold small metallic particles.
Neutralising – The part is then immersed in an alkaline solution to neutralise the etching acids.
Catalysing – A catalytic film is put on the surface to prepare for electroless metal plating.
Acceleration – This bath removes all the chemicals that remain and accelerates the catalysing film.
Electroless Plating – A thin deposit of nickel or copper is deposited on the plastic part.
Electro-Plating – A negative charge is applied to the part which is then dipped into a positively charged solution of the metal it is to be plated with. The positively charged metallic ions are attracted to the negatively charged part and then revert back to their metallic form. The part is removed from the solution and allowed to cool.
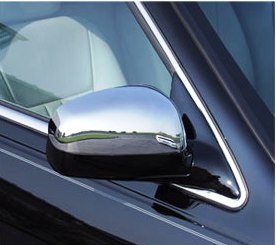
The most frequently used metals are chrome, nickel or gold. Applications include lamp reflectors, automotive interior and exterior parts (such as door handles), trims for dashboards, audio and video equipment, lightweight shower heads. Electroless plating may be used for cosmetics packaging, mobile phones, connector housings and shower heads.
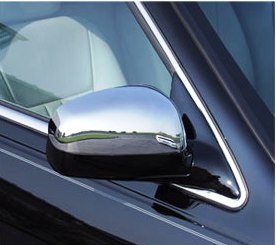