PipeSnug
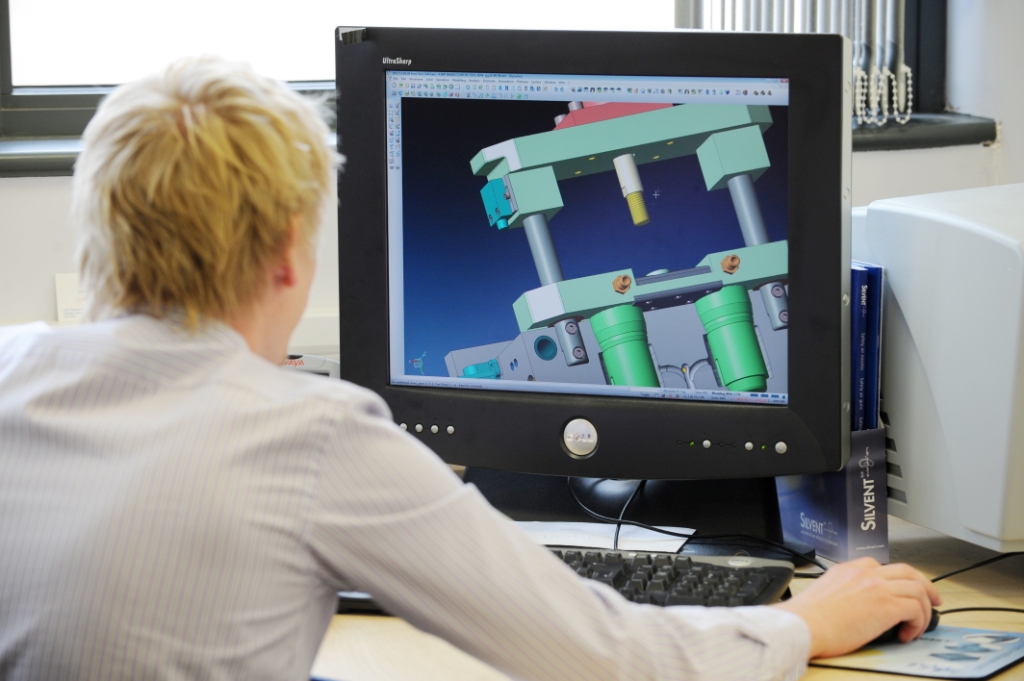
PipeSnug is the evolution of an idea that professionally qualified bricklayer and builder Chris Burdett, had to help solve a recurrent problem he encountered with his construction business. Making good around pipework can be a messy and time-consuming job, where you need to consider how much mortar to mix or silicone to use; especially if you are lugging it all up a ladder to make good at height.
Like all good ideas, PipeSnug is a simple but highly effective innovation designed to stop the mess, provide a neat finish and fast. It is designed to fit the elbow joint on 32 and 40mm waste pipes, once you have drilled the hole using a 52mm core drill. The product is pushed straight into the bored hole, giving a snug seal around the hole where a pipe exits a wall.
It looks smart, eliminates the need for mortaring or siliconing and it helps to maintain the energy efficiency of the property by tightly filling in any gaps where heat would
otherwise escape, and it keeps out vermin. PipeSnug was launched back in early 2017 and since then it has gone from strength to strength, with strong sales and a raft of innovation and Top Product awards.
‘’We started out with the basic idea and we know how the product needed to function, but we did not have an actual CAD so we were specifically looking for a manufacturer who could provide a concept to shelf solutions’’ commented Alex Lever, Burdetts business partner. ‘’We managed the preparation and research applying for patents and funding. Luckily we did not encounter any issues in the manufacturing process’’ added Lever.
Lever’s last comment is a source of affirmation for SImon Grainger, Design and product engineering manager at Rutland Plastics, Grainger worked on the product, refining the design and project managing it. “Being involved very early in the design process helped us to de-risk the project. We planned for every possible issue in terms of what could cause a problem. Carrying out a failure modes and effects analysis (FMEA) was crucial to the manufacturing success of this overmoulded part, as was the close working relationship we had with the material supplier and toolmaker.”
The part’s function and application mean that the exterior disc needs to be rigid, colourfast and weatherproof and the seal element must have flexibility. To negate the need for assembly an overmoulding method of production was chosen. Overmoulding is a process of producing a single part from two seperate thermoplastic materials, generally moulding a component in rigid plastic known as a substrate and in a second phase the pre-moulded component is loaded into a second tool and moulded over with a softer, flexible rubber-like plastic. Rutland Plastics used a polypropylene (PP) and thermoplastic elastomer (TPE) respectively.
Because the overmould material (TPE) would be flowing over a pre-moulded substrate (PP) there was concern that relying solely on a chemicalbond bond between the two materials may not achieve satisfactory results and without any guarantee for the outcomes, a mechanical interlock design was added with the option to remove it if unnecessary; this involved a series of undercuts in the substrate component that would allow the overmould to flow in and provide a failsafe solution. However, first-off samples proved the chemical bonding strong enough to eliminate the mechanical interlock from the design.
“Overmoulding is an efficient process to connect two materials, essentially two parts without assembly, and it was the right solution for PipeSnug. Because we were involved at the conceptual stage, it meant that our technical expertise was fully exploited, and we were able to engage the material suppliers from the start and benefit from their input. They carried out mouldflow3D analysis to advise on gate size and location. Our practice of working in complete partnership with all stakeholders, combined with our structured approach to assessing potential failures through FMEA ensured that PipeSnug’s journey to market was exactly as Alex stated – issue-free”, concluded Grainger.
The PipeSnug range has since extended to include a number of colour options and a 110mm (or 4”) wastepipe version. Burdett and Lever are currently working on other products, all of which are focused on solving problems in the construction and plumbing sector.
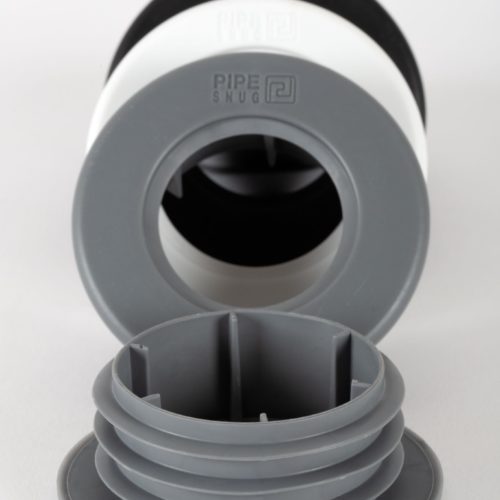
RECENT CASE STUDIES
Free design guide
"*" indicates required fields