DESIGN FOR MOULDABILITY (PART 1)
The aim for the most cost effective solution is to design parts in their finished form, i.e. without the requirement for secondary operations and with no waste of materials.
ADVANTAGES OF INJECTION MOULDING
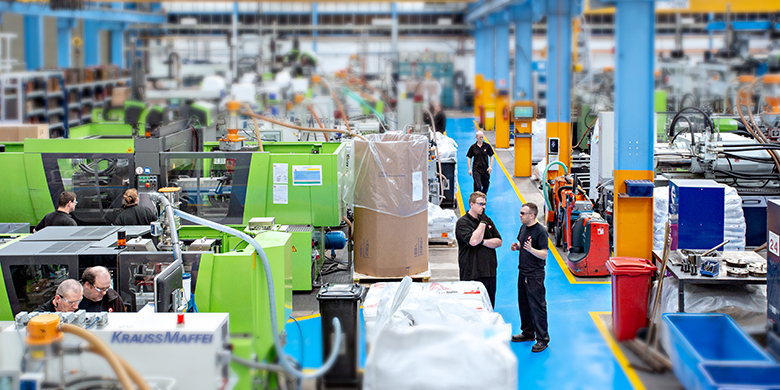
- Production of highly complex parts is possible
- Tight tolerances are repeatable
- Features such as bosses, snap-fits, undercuts and holes can be moulded in
- High quality surface properties are possible
- Automation is easier on long production runs
DESIGN CONSIDERATIONS
However, when considering injection moulding there are various design considerations:
- Nominal Wall Thickness – The ‘Goldilocks’ rule should apply – not too thick and not too thin
- Radii – Sharp corners should be avoided as these increase stress in a moulded part
- Ribs – Correct rib design is essential to achieve the right balance between strength and aesthetics
- Bosses – Correct design is essential for optimum strength and appearance
- Undercuts – To be avoided if possible
- Coring – Elimination of material from a particular area of the component to reduce wall thickness and material content
- Draft Angles – To facilitate part removal from the mould
- Textures, Lettering and Recesses – All design features that can enhance an injection moulded product or component
- Recesses – Not normally a problem but they can impact on the flow of the plastic
NOMINAL WALL THICKNESS
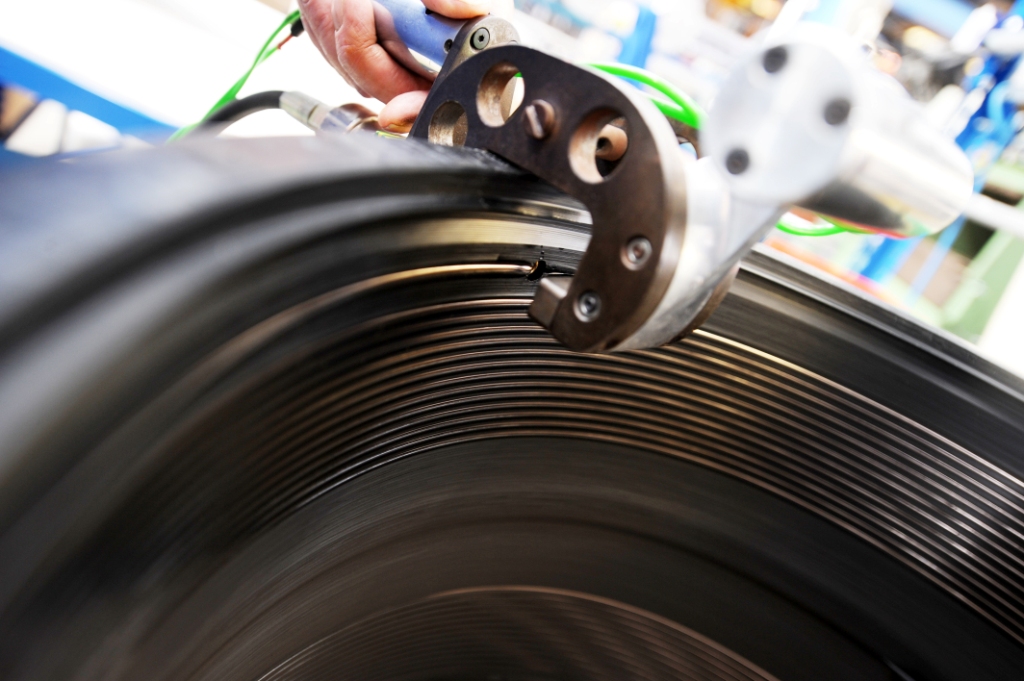
An important consideration in the design of any plastic injection moulded part is the wall thickness. A wall section that is too thin can lead to structural failure or poor insulation characteristics.
A wall section that is too thick can result in appearance defects and an overweight or over-engineered part. With the latter point it is also worth remembering that wall thickness governs the moulding cycle time – the thicker the section the longer the cycle time and therefore the more expensive the part becomes. Furthermore, plastics shrink during cooling which in thick sections can result either in the surface of the part forming a sink mark or an internal void.
In most applications a thin, uniform wall with ribs is preferable to a thick wall. There are general guidelines for how thick a part should be, typically 0.75mm to 3mm for filled materials and 0.5mm to 5mm for unfilled. However, this does depend on the design and function of the part concerned. It is possible to mould much thicker sections, if required. Rutland Plastics has successfully moulded void free parts up to 120mm thick.
Gas Assisted Injection Moulding can be used in some instances where ribbing is not possible or desired. Chemical foaming agents are also an option with thick section mouldings.
Where changes in thickness occur the aim should be to have the flow of the material from a thicker to a thinner section. Sharp corners should also be avoided as they cause stress which could lead to failure of the component. In cases where the thickness of a part must be increased, this should be less than 25%.
RADII
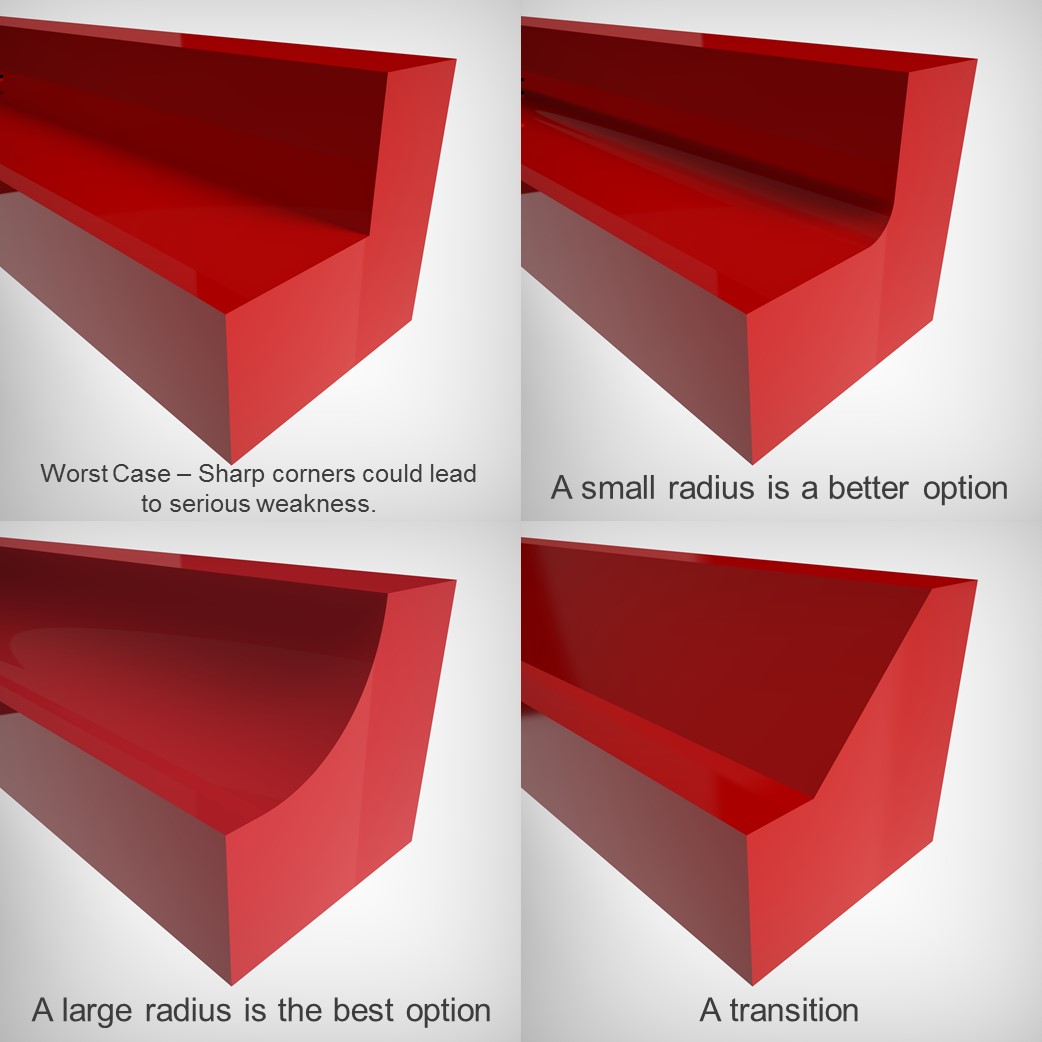
Radii are important to alleviate stress in the part. Generous radii should be used in areas of major change in section or direction. Furthermore, sharp corners should be avoided because:
- Facilitates ejection of the part from the mould. Sharp internal corners tend to stick in the mould as the part shrinks onto the core
- Provides smooth flow. Resin flows more easily around smooth radiused corners than sharp ones
- Reduces shear. Shear around sharp corners can degrade the material and cause aesthetic problems
An internal radius should be at least half the wall thickness and preferably in the range of 0.6 to 0.75 times wall thickness. However, this can result in a thicker section at the corner which goes against what was stated in the previous section. The result can be longer cycle times and a greater risk of distortion and sink marks. In an ideal situation the internal radius should be matched externally so maintaining a constant section.
Where a rib meets a wall there should be a radius on both corners. Again, this will result in a thickening of the wall at this point. There are various options in such circumstances (see article Design for Appearance).
FURTHER READING OR LINKS TO ALL GUIDES?
- Design Guide
- Design Development
- Design For Appearance
- Design For Assembly 1
- Design For Assembly 2
- Design For Assembly 3
- Design For Cost Consideration
- Design For Economy
- Design For Mouldability 1
- Design For Mouldability 2
- Design For Mouldability 3
- Design For Precision
- Design For Recyclability
- Design For Stiffness
- Design For Strength
- Design For Time
- Design Summary
- Flame Retardancy
- Flexibility
Free design guide
"*" indicates required fields